Impacts of loading, racking and inventory upon energy usage and temperature performance
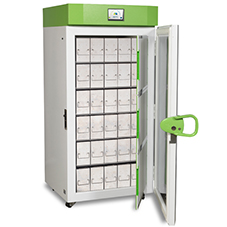
Part of ULT freezer best practice is the use of racking (aluminium or stainless steel) in combination with an inventory, also referred to as a ‘freezer map’ (see diagram 1). By employing these actions, end users can minimise door opening times — reducing both the associated energy consumption and temperature rises associated with retrieving and placing contents within the freezer.
A recent study[1] by independent laboratory sustainability specialist, Green Light Laboratories demonstrates the positive impact of these best practices in typical laboratory conditions.[2] This case study investigated the use of ULT freezer racking and basic inventory solutions, and their effects upon temperature performance and energy consumption.
The full case study is available on request, but we have summarised the key findings for you here.
- Part 1) The impact of racking on energy consumption and performance.
- Part 2) The impact of inventory on energy consumption.
Read part 1 of the case study here.
Please contact us at salesuk@calibrescientific.com if you would like more information on this case study or wish to discuss your cold storage requirements.
ULT Freezer Inventory Study
Part 2) The impact of inventory management on energy consumption
Testing conditions
A Stirling Ultracold SU780XLE 780 litre ULT freezer was filled (to 79% capacity) with 475 cryoboxes and water (in lieu of samples). A multi-probe wireless monitoring systems was used to measure temperature data. The racked freezer was installed with aluminium racking.[3]
End users from the Learning and Research Centre, University of Bristol were tasked with retrieving and returning named cryoboxes and later specific items.[4] The access times were measured for organised access (using a freezer map – see diagram 1), and unorganised access (without a freezer map).
Three scenarios were investigated:
- Unracked freezer, organised (with a freezer map)
- Racked, organised (with a freezer map)
- Racked, unorganised (no freezer map)
Diagram 1)
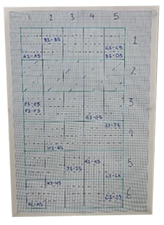
1) Effect of inventory management on energy usage and time
Figure 1)
Organised and unorganised access data from the SU780XLE at the -80 °C setpoint.

Finding: The use of basic inventory management (freezer map) had a clear positive effect on both the time taken to locate/relocate samples, and therefore on the energy used.
Racked freezer, organised versus unorganised:
- Energy used: 70% less energy used in racked, organised unit.
- Time saved: 67% less time used to locate/relocate samples in the racked, organised unit.
- When the ULT freezer was racked but had no inventory to guide end users, the total door opening time increased by 307%, consuming an extra 2.214 kWh.
The energy saved from just 3-4 days of organised door openings of a racked SU780XLE would save enough energy to operate it for 24 hours.[5]
2) Effect of racking on energy usage and time
Figure 2)
Organised freezer, racked and unracked access data from the SU780XLE at the -80 °C setpoint.

Finding: When utilising a freezer map, the addition of racking had a positive effect on both the time taken to locate/relocate samples and energy consumption. Figure 2) shows that by using racking in addition to an inventory reduces energy usage by >50%.
Organised freezer, racked versus unracked:
- Energy used: 56% less energy used in racked, organised unit.
- Time saved: 33% less time used to locate/relocate samples, in racked, organised unit.
- When the freezer was organised but not racked, the total door opening time increased by 149%, consuming an extra 1.188 kWh.
The energy saved by the addition of racking is enough to operate a lab grade 300 L fridge at 4 °C for over 24 hours and almost enough energy to power a ~400 L lab grade freezer at -20 °C for 24 hours.[6]
Finding: It will be reassuring to end users that even with long periods of door openings, the racking ensured that the warmest temperature recorded was -63.4 °C, measured in the top compartment. All other compartments remained below -70 °C. These results indicate that within the Stirling Ultracold SU780XLE freezer, highly temperature sensitive samples would be better stored in compartments 2-6.
On reflection:
It is likely that an organised, but unracked freezer will become increasingly untidy with repeated/frequent access. So, the benefits of racking on reducing door opening times would probably increase over time. In fact, Emma Foose (Core Facility Technician, Deputy Radiation Protection Supervisor / Freezer Manager (L&R), Bristol Medical School) stated:
“Many of our research groups use the ‘unracked but organised’ method for their freezers, usually by using a variety of plastic boxes. In theory this works fine, but taking part in the case study highlighted just how unorganised this method can be. Searching for a singular item can cause much disarray and longer door opening times. This is due to the need to reorganise, which is either done immediately, or more commonly is left for a later date. Usually this has a snowball effect causing increasing disorganisation, resulting in the requirement for a sorting session. These sorting sessions often keep the freezer open for long periods of time, at least 10 minutes if not 20-30 minutes. This puts extra strain on the freezer, causes ice build-up, often makes a mess on the floor, and most concerningly can degrade the samples in the freezer.”
This case study is also useful in highlighting the realistic length of freezer door openings for those using no inventory or a basic inventory. The quickest door opening time to retrieve two cryoboxes was: 40 seconds for an organised, racked freezer and 120 seconds for a racked but unorganised freezer. This provides a useful benchmark when end users are considering door opening recovery data supplied by freezer manufacturers and other organisations, such as ENERGY STAR.[7] This study suggests that door opening times are likely to be at least 40 seconds for freezers that contain many samples.
In summary:
This study by Green Light Laboratories shows the positive impact of simple freezer inventory management in typical laboratory conditions. Using basic inventory management:
- Shortens door opening times, saving up to 67% in time
- Reduces door opening energy usage, saving up to 70%
Using aluminium freezer racking in combination with basic inventory management:
- Reduces door opening times by 33%
- Lowers energy consumption of door openings by more than 50%
Please contact us at salesuk@calibrescientific.com if you would like more information on this case study.
[1] Green Light Laboratories study: ULT FREEZER INVENTORY STUDY, 2024: Full Case Study available on request.
[2] Location: Learning and Research Centre, University of Bristol. The laboratory space used was air conditioned with an ambient temperature of 23 °C (±1.5 °C).
[3] 114 kg of aluminium racking (x30 racking units).
[4] Full protocol available on request.
[5] Energy used in 24 hours for a racked SU780XLE without any door openings.
[6] https://www.medlinescientific.co.uk/sustainable-solutions/refrigeration/
[7] ENERGY STAR door opening test methods (2014): Door left open for 15 second (using 2 seconds to open and 2 seconds to close; plus 2 seconds to open the inner door open and 2 seconds to close it) = 23 seconds door opening: https://www.energystar.gov/sites/default/files/ENERGY%20STAR%20V1.1%20Lab%20Grade%20Refrigerator%20and%20Freezer%20Program%20Requirements.pdf