Impacts of loading, racking and inventory upon energy usage and temperature performance
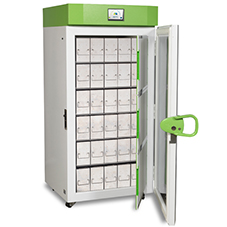
Part of ULT freezer best practice is the use of racking (aluminium or stainless steel) in combination with an inventory, also referred to as a ‘freezer map’ (see diagram 1). By employing these actions, end users can minimise door opening times — reducing both the associated energy consumption and temperature rises associated with retrieving and placing contents within the freezer.
A recent study[1] by independent laboratory sustainability specialist, Green Light Laboratories demonstrates the positive impact of these best practices in typical laboratory conditions.[2] This case study investigated the use of ULT freezer racking and basic inventory solutions, and their effects upon temperature performance and energy consumption.
The full case study is available on request, but we have summarised the key findings for you here.
- Part 1) The impact of racking on energy consumption and performance.
- Part 2) The impact of inventory on energy consumption.
Please contact us at salesuk@calibrescientific.com if you would like more information on this case study or wish to discuss your cold storage requirements.
ULT Freezer Inventory Study
Part 1) The impact of racking on energy consumption and performance
Testing conditions
A Stirling Ultracold SU780XLE 780 litre ULT freezer was filled (to 79% capacity) with 475 cryoboxes and water (in lieu of samples). A multi-probe wireless monitoring systems was used to measure temperature data. The racked freezer was installed with aluminium racking.[3]
Diagram 1)
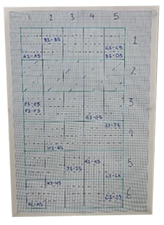
1) Performance data: Energy usage
Figure 1)
Energy performance data of the SU780XLE at -80 °C setpoint in two different loading configurations. Units were 79% full.

Finding: Installing aluminium freezer racking had a negligible effect on energy usage of a 79% full freezer. The racked unit consumed 0.06 W/L/day (0.052 kWh/day) more than the unracked freezer. This equates to <1% increase in energy consumption.
2) Effect of racking on freezer warm up times
Figure 2)
Warm up times of the SU780XLE to -50 °C with and without racking from the -80 °C setpoint. Each compartment was measured; the lowest and highest warm up times are included below.

Finding: Although warm up times varied between freezer compartments, the use of racking had an ameliorative effect on freezer warm up times.
In fact, racking provided at least 20% more time before the -50 °C threshold was reached following the units being turned off. The warm up times to -50 °C were increased by between almost 5 hours and 7.63 hours, depending on the compartment.
The increased warm up time would provide users with valuable extra time during a power outage to relocate the unit to a different freezer room or transfer samples to a back up freezer.
3) Effect of racking on door opening (DO) energy usage
Figure 3)
Energy performance data on door opening of the SU780XLE at the -80 °C setpoint in two different loading configurations. Timed DOs of 60 seconds and 90 seconds were carried out with the energy consumed measured. The table below shows the combined energy used for a single 60-second and a single 90-second DO.

Finding: The freezer with racking consumed less energy than the unracked unit. With aluminium racking in place, the SU780XLE used 18% less energy with a single 60-second and a single 90-second DO.
Even for a modern energy efficient freezer such as the SU780XLE, this reduction would assist busy laboratories in their efforts to conserve energy usage throughout the lifetime of the freezer.
4) Effect of racking on temperature recovery after DO
Timed DOs of 60 seconds and 90 seconds were carried out with the energy performance measured in each compartment (full data available on request).
Finding: The temperature recovery after both the 60s and 90s DO was rapid in most probe locations within the 79% full Stirling Ultracold freezer — both with and without racking in place. In the majority of probe locations, temperature recovery took less than a minute.
However, something to consider when loading more temperature sensitive samples in a racked freezer: In this particular study, temperature recovery after the 90s DO was slower in the top compartment. This is likely due to warmer air getting ‘trapped’ towards the top of the freezer.
5) Effect of racking on temperature stability after DO
Figure 4)
Temperature performance data of the SU780XLE at the -80 °C setpoint in two different loading configurations. Data below is for a single 60s DO.

Finding: Racking had a positive impact on temperature stability within the freezer upon door opening. The temperature increase was lower with racking in place in almost every probe location.
It should be noted, that even without racking in place the Stirling Ultracold unit demonstrated good temperature stability:
In all probe positions, in both the racked and unracked freezer, the temperature remained safely below -70 °C at all times, after 60s and 90s DO.
On reflection:
Previous racking studies[4], also conducted by Green Light Laboratories, have demonstrated the positive impact of racking on ULT freezer temperature stability upon door opening and on warm up times to -50 °C. However, those studies also showed that installing racking increased the energy usage of door openings and the temperature recovery times.[5] These case studies investigated the effect of racking on the performance of an empty freezer.
In contrast, this latest study with a 79% full freezer demonstrated that both the energy usage and temperature recovery time, on door opening are better for freezers that have racking installed compared to those that don’t. This is in line with the concept that, once setpoint temperature is achieved, full freezers run more efficiently than empty ones.
In summary:
This study by Green Light Laboratories shows the positive impact of freezer racking in typical laboratory conditions. The use of aluminium freezer racking:
- Increases freezer warm up to -50 °C times by at least 20%
- Reduces energy consumption by up to 18% for timed door openings
- Improves temperature stability on door opening
Check out part 2 of the case study here, or you can contact us at salesuk@calibrescientific.com if you would like more information on the case study.
[1] Green Light Laboratories study: ULT FREEZER INVENTORY STUDY, 2024: Full Case Study available on request.
[2] Location: Learning and Research Centre, University of Bristol. The laboratory space used was air conditioned with an ambient temperature of 23 °C (±1.5 °C).
[3] 114 kg of aluminium racking (x30 racking units).
[4] Green Light Laboratories Study: ULT FREEZER RACKING STUDY (2018) and ULT FREEZER RACKING STUDY – PART II (2019).
[5] In the empty unracked ULT freezer, door openings used 0.78 kWh of electricity. In the freezer with aluminium racking, these door openings used 1.27 kWh. For 60, 90, and 120 second door openings, the freezers with aluminium racking and stainless steel racking took twice as along to recover their temperature. Full data available on request.